Our Latest News
ATC at Advanced Materials 2025
Visit ATC & Monmouth Scientific on Stand 1243 at Advanced Materials 2025 to explore sustainable cooling & clean air solutions for advanced materials research.
Using Water Safely
Water is an effective and affordable coolant—but only when used correctly. Here are 10 essential things to consider before using water in your cooling system.
World Environment Day
Cooling responsibly: Read more about how ATC reduces plastic waste with smarter packaging, durable chillers, scrappage schemes, and eco-friendly cooling solutions
Earth Day Spotlight
Discover how low-GWP refrigerants, leak-free chillers, and water-saving cooling systems from ATC help reduce environmental impact this Earth Day.
The Costly Cooling Conundrum
Stop costly water waste & equipment damage. Discover why switching from tap water to a closed cooling system is the smarter, sustainable way to save big today!
Who were Thermal Exchange?
Discover the legacy of Thermal Exchange, pioneers in industrial cooling, now part of ATC. Learn about their expertise in chillers, heat exchangers & UK manufacturing.
Navigating the Future of Refrigerants
Explore Applied Thermal Control’s proactive response to evolving refrigerant regulations. Learn about the Kigali Amendment, low-GWP refrigerants, manufacturing challenges, impacts on labs, and ATC’s innovative solutions, including new product lines and expanded global service capabilities.
Introducing Joe Bull
We are excited to welcome Joe Bull as our new Head of Engineering at Applied Thermal Control. With over 10 years of experience and a focus on transitioning to low-GWP refrigerants, Joe is already making significant contributions to our technical advancements. Welcome to the team, Joe!
Welcoming Jonathan Simmonds
ATC warmly welcomes Jonathan Simmonds as our new Quality Manager. With his appointment on 5th September 2023, Jonathan brings extensive experience and a commitment to elevating our quality management standards. He’s keen on advancing ATC’s quality assurance and looks forward to contributing to our growth.
Uniting for a cause
Applied Thermal Control is set to participate in the EuroProjects Charity Football Tournament at Ashby Leisure Centre on 1st September, in support of Loros Hospice. This event promises an afternoon of football, camaraderie, and the chance to make a meaningful difference for those in end-of-life care.
Faizaan Mulla Joins as Sales Executive
ATC welcomes Faizaan Mulla as the new Sales Executive, bringing a fresh perspective on customer engagement and a strong commitment to driving growth. With his passion for understanding customer needs and a background rich in sports and leadership, Faizaan is poised to make a significant impact at ATC.
Thermal Exchange Products Relocate
Thermal Exchange products are now conveniently available on the Applied Thermal Control website, following a strategic merging under the SDI Group umbrella. This thoughtful consolidation offers customers much easier access to a broad array of cooling equipment, significantly streamlining both customer service and operational efficiency.
Summer Maintenance
Maximise your recirculating chiller’s efficiency this summer with essential maintenance steps: clean regularly, check fluid levels, inspect for any leaks, ensure clear and unobstructed airflow, and closely monitor performance. Keep your cooling system operating at optimal levels; and don’t hesitate to contact us for expert support.
Spring Cleaning
As Spring arrives, it’s the perfect time to ensure your chiller operates optimally. Regular maintenance extends lifespan and optimises efficiency. The proactive maintenance measures outlined here are designed to mitigate unexpected downtime and reduce operational costs., safeguarding your investment.
Rhiannon Joins as Marketing Executive
Applied Thermal Control welcomes Rhiannon Owen as our new Marketing Executive. With a unique background in engineering enthusiasm and a career in education, Rhiannon applies her diverse skills to effectively communicate with customers and support our sales and technical teams.
Christmas Shutdown Protection
Preparing your chillers for the holiday downtime or a temporary shutdown? Implement these simple yet essential maintenance steps to ensure your systems are protected and primed for an effortless restart. Thorough cleaning and proper shutdown procedures are key to hassle-free operation upon your return.
UL Listed X-Ray Cooling Systems
Thermal Exchange Ltd, now under ATC, designed a specialized cooling system for a high-tech X-ray system. Overcoming obstacles in cooling efficiency, system monitoring, and compliance, the solution comprises a dual-unit setup for exact temperature control and consistent fluid flow, safeguarding the equipment’s performance.
ATC and Thermal Exchange synergy
The SDI Group has merged ATC and Thermal Exchange, enhancing chiller selection, service efficiency, and customer support. This strategic union aims to drive innovation with a broader product range and superior technical support, emphasising excellence in customer care and product reliability for all users.
Chiller Scrappage Scheme
ATC is dedicated to minimising environmental impact. Recognising the importance of responsible chiller disposal, ATC offers a scrappage scheme for the safe reclamation or disposal of refrigerants, particularly F-Gases. Contact ATC to contribute to a greener planet by responsibly disposing of your old chiller.
ATC appoint Sales Director
Applied Thermal Control warmly welcomes Ryan as its new Sales Director, following Job Abel’s retirement. Ryan, who initially began his career with Applied Thermal Control in 2012, returns armed with extensive experience, ready to strategically steer the company towards further growth under the SDI Group’s ownership.
UKAS Calibration
ATC announces all electrical and thermal inspection tools are now UKAS calibrated, meeting the United Kingdom Accreditation Service’s high standards. This commitment ensures quality, reliability, and excellence in manufacturing. Meeting ISO 9001 certification, ATC guarantees quality management and customer satisfaction.
ATC Supply RRS Sir David Attenborough
ATC has proudly supplied K4 recirculating chillers for the laboratory aboard RSS Sir David Attenborough, supporting the British Antarctic Survey’s critical polar research. This collaboration highlights ATC’s dedication to advancing scientific exploration and tackling environmental challenges.
SDI Acquisition of Thermal Exchange
SDI Group has acquired Thermal Exchange Ltd, enhancing its portfolio with advanced cooling and temperature control solutions for industrial, medical, and scientific sectors. This strategic move promises growth through synergy between Thermal Exchange and Applied Thermal Control, expanding product offerings and global reach.
Rooftop Recirculating Chillers
Loughborough University recently upgraded its Physics and Chemistry departments with ATC’s K3 chillers, strategically positioned on the roof to efficiently support advanced research equipment. This move highlights the university’s strong commitment to providing top-notch educational and cutting-edge research facilities.
UL Listed Chillers From ATC
ATC has embraced UL standards, partnering with Intertek to ensure our chillers conform to stringent safety and quality benchmarks. This initiative reflects our commitment to excellence and supports the needs of our international OEM customers, reinforcing our position in the global market.
Preventative Maintenance Contracts
Our expert technicians provide on-site inspections and maintenance, aimed at preventing breakdowns and extending equipment life. With flexible contracts and rapid UK response times, ATC’s maintenance service is designed to keep your operations running smoothly. Protect your investment and avoid downtime with ATC.
ATC Update ISO Accreditations
Applied Thermal Control proudly announces compliance with the 2015 revisions of ISO 9001 and ISO 14001 standards, underscoring our commitment to quality and environmental stewardship. These certifications highlight our dedication to maintaining high-quality practices and reducing our environmental impact.
SDI Group Acquisition of ATC
ATC has joined the SDI Group, aligning with SDI’s strategic focus on expanding its technology and product offerings in the life sciences and related markets. This acquisition enables ATC to leverage SDI’s resources to accelerate product development and expand its global presence, promising exciting growth and technological advancements.
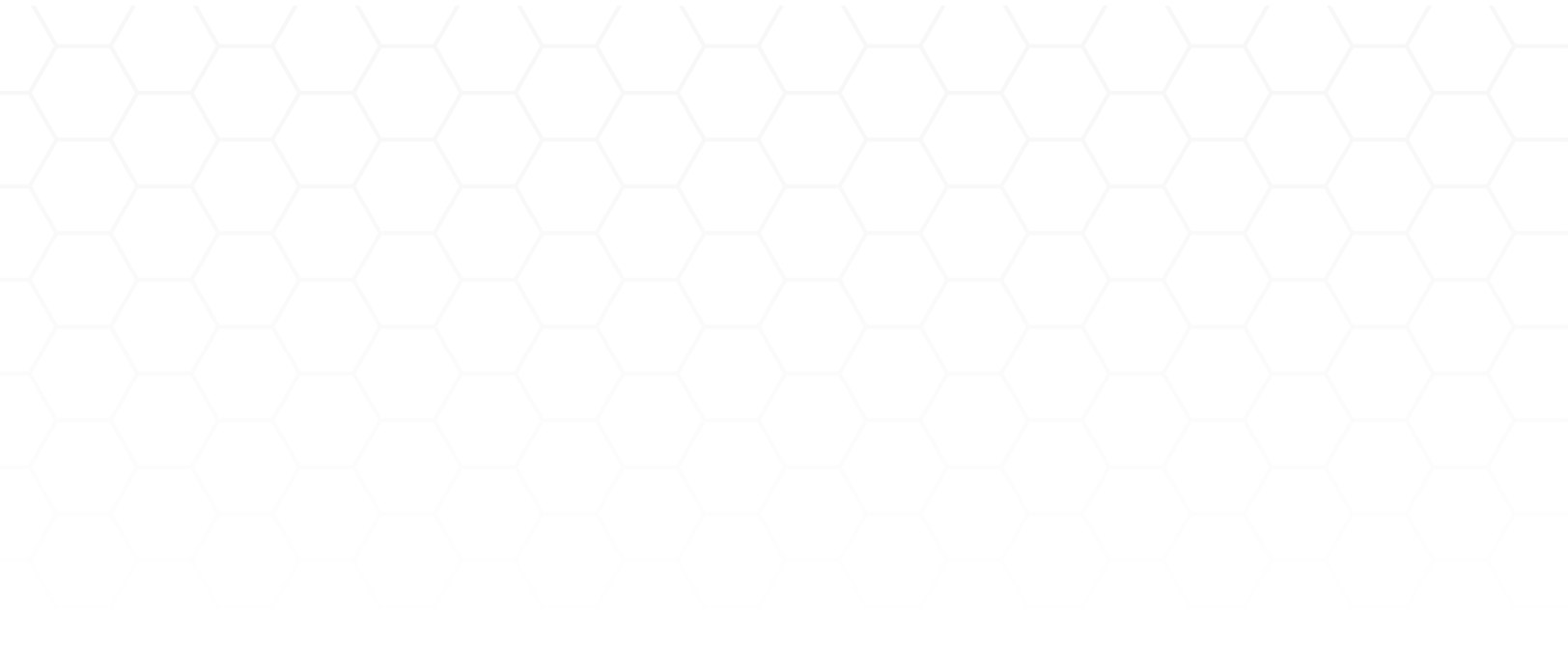