Posted: 19 June 2023
What are Nanomaterials?
Nanomaterials are materials that
have characteristic dimensions at the nanometre scale, typically ranging from 1
to 100 nanometres (nm). They exhibit unique properties and behaviours due to
their nanoscale dimensions, surface-to-volume ratio, and quantum effects.
Nanomaterials can be engineered or naturally occurring, and they may consist of
various substances, including metals, semiconductors, ceramics, polymers, or
composites.
Nanomaterials and Process Cooling
Process cooling plays a crucial
role in nanomaterial research and production by maintaining precise and
controlled temperatures during various stages of the process. Nanomaterial
synthesis often involved chemical reactions, physical transformations, or
deposition techniques that require specific temperature conditions. Some
examples of how process cooling equipment is used in nanomaterial research and
production include:
Chemical Synthesis
- Many nanomaterials are
synthesised through chemical reactions that involve heating or cooling steps.
Process cooling equipment, such as chillers, are used to control the
temperature during these reactions. Cooling can be required to maintain a
specific temperature range for the reactants or to facilitate the
crystallisation of the nanomaterial. Cooling is especially important in
controlling the growth rate, particle size, and morphology of the nanomaterial.
Precursor Deposition
- In processes like chemical
vapour deposition (CVD) or physical vapour deposition (PVD), cooling is
utilised to maintain the desired temperature of the substrate or deposition
chamber. Cooling equipment helps to remove heat generated during the deposition
process, preventing excessive temperature rise and ensuring the stability of
the process. This control is critical for achieving uniform and high-quality
nanomaterial coatings or thin films.
Solvent Evaporation
- In nanoparticle synthesis
or thin film deposition, solvents are often used to dissolve or disperse the
nanomaterial precursor. Process cooling can be employed to control the rate of
solvent evaporation. By cooling the system, the solvent evaporates at a slower
rate, allowing for controlled precipitation or deposition of the nanomaterial
particles or films. This control is crucial for obtaining desired particle
sizes, dispersion, or film thickness.
Material Processing
- Cooling is often utilised
during material processing steps, such as milling, grinding, or sintering, which
are common in nanomaterial research and production. Cooling equipment can help
to dissipate the heat generated during these processes, preventing thermal
damage or excessive agglomeration of nanoparticles. Controlled cooling allows
for more precise control over particle size distribution, mechanical
properties, and structural characteristics.
Instrumentation and Characterisation
- Cooling is essential for
maintaining stable temperatures during the characterisation and testing of
nanomaterials. Techniques such as scanning electron microscopy (SEM),
transmission electron microscopy (TEM), or thermal analysis require controlled
temperatures for accurate measurements. Cooling equipment can be used to cool
sample holders, stages, or chambers, ensuring stable conditions and reliable
characterisation results.
Recirculating Chillers
Chillers are widely utilised in
nanomaterial research and production for temperature control. Some of the key
benefits of their use include:
Temperature stability:
- Recirculating chillers
ensure precise and stable temperature control, which is crucial for the
synthesis and processing of nanomaterials. Maintaining a consistent temperature
throughout the process helps to achieve reproducible results and ensures the
reliability of experimental data. Temperature fluctuations can affect the size,
morphology, and properties or nanomaterials, making precise temperature control
essential.
Process optimisation:
- Recirculating chillers
allow researchers and manufacturers to optimise the synthesis and processing
conditions by providing the flexibility to adjust and control temperatures.
Different nanomaterials may require specific temperature profiles for growth,
crystallisation, or phase transformations. Chillers enable precise tuning of
temperatures to achieve desired material properties and characteristics.
Cooling capacity:
- Chillers provide efficient
cooling capacity, which is essential for dissipating the heat generated during
nanomaterial synthesis and processing. Certain reactions or deposition
processes can generate significant amounts of heat, and effective cooling is
necessary to prevent overheating, maintain stability, and prevent thermal
damage to the nanomaterials or equipment.
Wide temperature range:
- Recirculating chillers are
available in a wide temperature range, allowing researchers and manufacturers
to cool materials and processes to specific temperatures, from sub-zero
temperatures to elevated temperatures. This flexibility is valuable for various
nanomaterial synthesis methods, including sol-gel processes, hydrothermal
synthesis, or thermal annealing.
Process efficiency:
- Efficient cooling provided
by chillers reduces the overall process time by facilitating rapid heat
removal. Quicker cooling rates can lead to improved productivity and higher
throughput in nanomaterial production. Additionally, efficient cooling helps to
maintain the stability and reliability of processes, reducing the likelihood of
defects or variations in the final nanomaterial products
Equipment protection:
- Recirculating chillers play
a role in protecting equipment used in nanomaterial research and production. By
maintaining optimal temperatures, they prevent excessive heat accumulation,
which can lead to premature equipment failure or damage. Chillers help to
extend the lifespan of reactors, deposition chambers, and other critical
equipment, ensuring consistent performance and reducing maintenance costs.
Heat Exchangers
Nanomaterial research and
production processes can benefit from heat exchangers, which provide similar
advantages as a recirculating chiller, but at a lower initial cost and with
reduced energy consumption. Some specific advantages of the use of heat
exchangers in relation to nanomaterial research and production include:
Efficient heat dissipation:
- Heat exchangers are
designed to efficiently transfer heat between fluids or between a fluid and the
environment. In nanomaterial research and production, various processes
generate heat, such as chemical reactions, nanoparticle synthesis, or material
processing steps. Heat exchangers effectively remove excess heat, preventing
overheating and maintaining stable operating conditions.
Temperature control:
- Heat exchangers provide
temperature control by removing or adding heat as required. They help to
maintain optimal temperatures during nanomaterial synthesis, processing, or
characterisation, ensuring consistent results and reliable data.
Temperature-sensitive processes such as chemical vapour deposition (CVD) or
crystallisation, can benefit from a heat exchanger’s ability to maintain stable
temperature profiles.
Scalability:
- Heat exchangers are
scalable and can be designed to meet the cooling requirements of various
production scales, from laboratory-scale research to industrial manufacturing.
They can be integrated into production systems, reactors, or process equipment,
accommodating different volumes and flow rates. Heat exchangers allow for
efficient and controlled heat transfer regardless of the scale of the operation.
Prevention of thermal damage:
- Efficient heat transfer
provided by heat exchangers helps to prevent thermal damage to nanomaterials
and equipment. By dissipating excess heat, heat exchangers reduce the risk of
overheating, which can cause structural changes, agglomeration, or degradation
of nanomaterials. Heat exchangers contribute to maintaining the integrity and
quality of nanomaterial products.
Safety:
- Heat exchangers enhance
safety in nanomaterials research and production processes by maintaining
controlled temperatures and preventing temperature fluctuations. By providing
stable operating conditions, they minimise the risk of thermal hazards, such as
uncontrolled reactions or thermal runaway, improving the overall safety of the
operations.
The choice of process cooling
equipment depends on the specific needs of the nanomaterial research or
production process, including cooling capacity, temperature range, and
scalability. Often, a combination of different cooling techniques and equipment
is employed to achieve precise temperature control throughout the various
stages of nanomaterial synthesis, processing, and characterisation.
We are excited to be exhibiting at Advanced Materials 2023. Find us on stand 1418 for a chat about how we can support with your process cooling requirements.
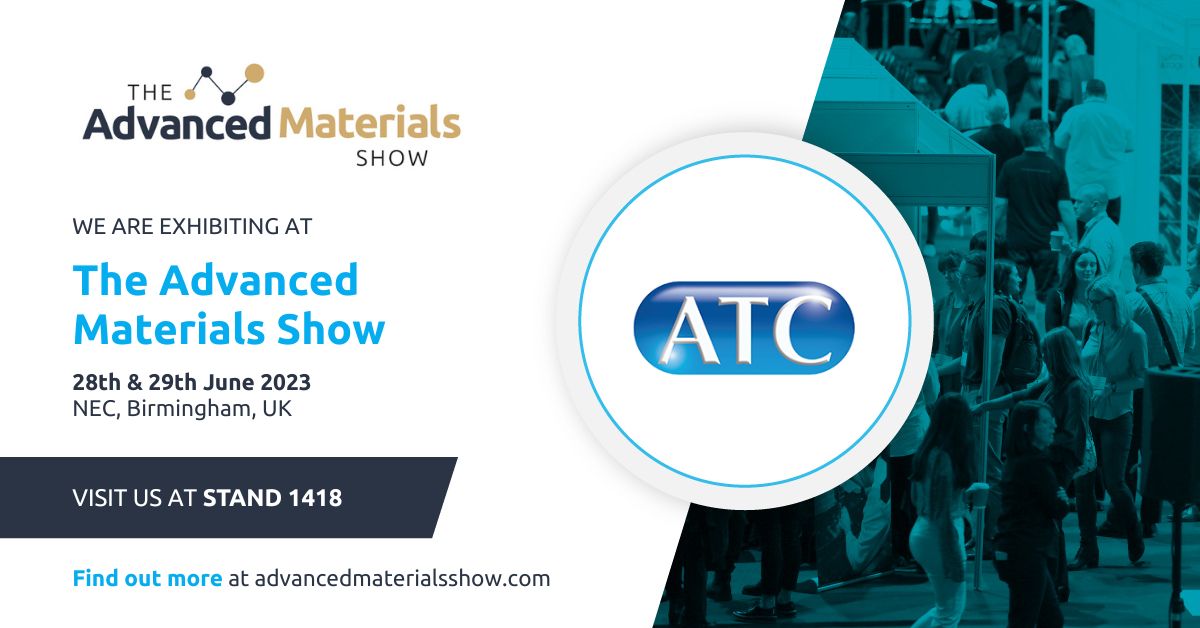