Posted: 15 June 2023
What is Graphene?
Graphene is a two-dimensional
carbon allotrope consisting of a single layer of carbon atoms arranged in a
hexagonal lattice pattern. It is the basic structural element of other carbon allotropes
like graphite, charcoal, and carbon nanotubes. Graphene is considered a
remarkable material due to its exceptional properties, which include:
- Strength
- Flexibility
- Electrical conductivity
- Thermal conductivity
- Transparency
- Impermeability
- Large surface area
Graphene and Process Cooling
Process cooling equipment plays
a crucial role in graphene production and research by maintaining optimal
operating temperatures during various stages of the process. Graphene is
typically produces through methods such as chemical vapour deposition (CVD) or
exfoliation, which involve precise control of temperature to achieve
high-quality graphene with desired properties. Some examples of how process
cooling equipment is used in graphene production and research include:
Chemical Vapour Deposition (CVD)
- In CVD, a substrate is
exposed to a carbon-containing gas at high temperatures. The process cooling
equipment is used to regulate and maintain the temperature of the substrate or
reaction chamber. This is important because temperature influences the growth
rate, crystal structure, and quality of the graphene layer. Cooling equipment,
such as chillers, can provide precise temperature control, ensuring consistent
and controlled growth of graphene layers.
Liquid Cooling Systems
- Liquid cooling systems are
often employed in graphene research and production to cool down different
components involved in the process. For example, cooling systems may be used to
cool the reaction chamber, gas lines, or the substrate holder. By removing
excess heat, these systems help to maintain stability and prevent thermal
fluctuations that could affect the growth and properties of graphene.
Cooling During Exfoliation
- In the exfoliation method,
graphene is obtained by mechanically or chemically exfoliating graphite.
Cooling equipment can be used during the exfoliation process to control the
temperature and improve the quality of the resulting graphene. Cooling can aid
in reducing the heat generated during exfoliation, which may lead to better
control over size, thickness, and quality of the exfoliated graphene flakes.
Cooling for Characterisation and Testing
- Graphene samples often need
to undergo various characterisation techniques and testing. Some of these
techniques, such as Raman spectroscopy or electrical measurements, require
precise temperature control. Process cooling equipment can be employed to
maintain stable temperatures during these measurements, ensuring accurate and
reliable results.
Recirculating Chillers
Recirculating chillers are
widely utilised in graphene production and research to control and maintain the
temperature of various components and processes. Some of the key benefits of
the use of recirculating chillers in relation to graphene include:
Temperature stability:
- Recirculating chillers
ensure precise and stable temperature control, which is crucial for the
synthesis, processing, and characterisation of graphene. Graphene’s properties
can be highly sensitive to temperature variations, and maintaining a consistent
temperature throughout the process is essential for reproducibility and
reliable results. Recirculating chillers offer tight temperature control to
meet the stringent requirements of graphene research.
Cooling capacity:
- Recirculating chillers
provide efficient cooling capacity, capable of dissipating the heat generated
during graphene production processes. Graphene synthesis often involves
chemical vapour deposition (CVD) or other high-temperature processes that
generate substantial heat. Recirculating chillers efficiently remove the excess
heat, preventing overheating, and maintaining stable operating conditions.
Precise temperature control:
- Recirculating chillers
offer precise temperature control over a wide range, allowing researchers and
manufacturers to achieve and maintain the specific temperatures required for
graphene synthesis and processing. This precise temperature control is critical
for controlling the growth, quality, and properties of graphene, as well as for
optimising the process parameters.
Scalability:
- Recirculating chillers can
be utilised in both laboratory-scale research and industrial-scale production
of graphene. They can be integrated into various setups, such as CVD systems or
reaction chambers, accommodating different volumes and production scales.
Recirculating chillers provide consistent and reliable cooling, regardless of
the scale of the operation.
Ease of use and Maintenance:
- Recirculating chillers are
designed for ease of use and maintenance. They typically come with
user-friendly interfaces and controls that allow researchers and operators to
set and monitor temperature parameters easily. They often have built-in safety
features, alarms, and system diagnostics, making them reliable and convenient
for graphene research and production processes.
Compact and space-saving design:
- Recirculating chillers are
compact and space-saving, which is advantageous, particularly in laboratory
settings where space may be limited. Some models can be easily placed on
laboratory benches or integrated into existing setups without requiring
significant space allocation.
Reduced water consumption:
- Recirculating chillers
employ closed-loop systems that minimise water consumption. By recirculating
and reusing heat transfer fluids, they reduce the need for continuous water
supply and discharge. This water-saving feature is environmentally friendly and
helps to reduce overall operational costs.
Heat Exchangers
Heat exchangers offer similar benefits
in graphene research and production processes to that of a recirculating
chiller but with lower initial cost and reduced energy consumption,
contributing to efficient heat transfer, temperature control, and the overall
quality of graphene materials. Some specific advantages of their usage in
relation to graphene research and production include:
Temperature control:
- Heat exchangers enable
temperature control, which is crucial in graphene synthesis and processing.
Graphene production methods, such as chemical vapour deposition (CVD), require
specific temperature profiles to achieve high-quality graphene layers. Heat
exchangers help to maintain stable temperatures, ensuring consistent growth
conditions and control over the graphene’s properties.
Efficient heat dissipation:
- Heat exchangers efficiently
remove excess heat generated during the graphene synthesis process. CVD
processes, for example, involve the decomposition of carbon-generation. Heat
exchangers facilitate efficient cooling, preventing overheating and minimising thermal
gradients across the graphene layers.
Thermal stability:
- Graphene is highly
sensitive to temperature changes, and maintaining thermal stability is crucial
for preserving its structural integrity and properties. Heat exchangers provide
effective heat transfer, preventing localised temperature variations that could
lead to defects or undesirable structural changes in graphene. Stable
temperatures ensure consistent quality and performance of graphene materials.
Scalability:
- Heat exchangers can be scaled
up to meet the cooling demands of large-scale graphene production. As the
demand for graphene increases, industrial-scale production methods are being
developed. Heat exchangers can be integrated into large-scale reactors or
deposition systems, providing efficient cooling capacity to handle higher
volumes of graphene production.
Preventing oxidation:
- Graphene is susceptible to
oxidation at high temperatures or in the presence of oxygen-containing
environments. Heat exchangers assist in controlling the graphene production
environment by maintaining inert atmospheres or low oxygen levels, minimising
the risk of graphene oxidation during synthesis and processing. This helps
preserve the high-quality and desired properties of graphene.
Process optimisation:
- Heat exchangers offer
flexibility in optimising graphene production processes, By precisely
controlling temperature profiles, researchers can fine-tune growth parameters,
such as cooling rates or annealing temperatures, to optimise the graphene’s
properties, including layer thickness, crystallinity, and electronic
characteristics. Heat exchangers enable reproducibility and consistency in
graphene production.
Equipment protection:
- Heat exchangers help to
protect equipment used in graphene research and production by dissipating
excess heat. Effective cooling minimises the risk of equipment damage due to
thermal stress and prolongs the lifespan of reactors, deposition systems, and
associated components. Heat exchangers contribute to the reliability and longevity
of the equipment used in graphene production.
It is important to note that the
specific cooling equipment used may vary depending on the requirements of each
graphene production or research facility. Different methods and setups may
necessitate different cooling strategies, and a combination of multiple cooling
techniques may also be employed in some cases.
We are excited to be exhibiting at Advanced Materials 2023. Find us on stand 1418 for a chat about how we can support with your process cooling requirements.
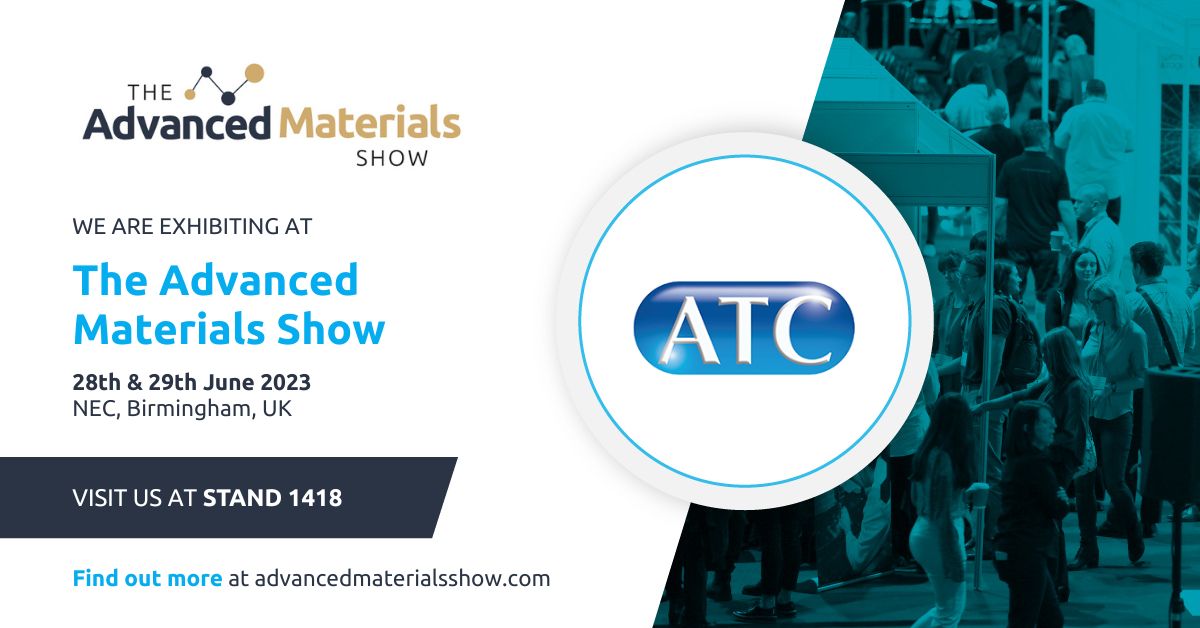