Posted: 23 June 2023
What are Advanced Coatings?
Advanced Coatings refer to a
category of specialised coatings that offer enhanced properties and
functionalities beyond traditional coatings. These coatings are designed to
provide superior protection, performance, durability, and other desirable
characteristics in various applications. Advanced coatings typically
incorporate advanced materials, technologies, and formulations to achieve
specific objectives. They can be used in a wide range of industries, including
automotive, aerospace, electronics, energy, construction, and more. Some common
types and characteristics of advance coatings include:
- Protective coatings
- Functional coatings
- High-temperature coatings
- Conductive coatings
- Optical coatings
- Anti-corrosion coatings
- Nanostructured coatings
Process Cooling and Advanced Coatings
Process cooling equipment plays
a crucial role in advanced coatings research and production by providing
efficient cooling to maintain optimal temperature conditions during coating
processes. Some examples of how process cooling equipment is utilised in
relation to advanced coatings are below:
Temperature Control
- Advanced coatings often require
precise temperature control during application, curing, or drying processes. Process
cooling equipment, such as chillers or heat exchangers, is used to regulate and
maintain the desired temperature. By removing excess heat generated during the
coating processes, cooling equipment helps to control the coating’s viscosity,
curing rate, and overall quality.
Viscosity Control
- The viscosity of the
coating material can significantly impact its application and performance.
Process cooling equipment helps to control the temperature of the coating
material, thereby influencing its viscosity. By cooling the coating material,
the equipment can increase its viscosity, allowing for better control during
application and reducing the risk of drips, sags, or uneven coating thickness.
Solvent Evaporation
- Many advanced coatings
contain solvents that need to evaporate during the curing or drying process.
Process cooling equipment aids in the evaporation of these solvents by
maintaining a controlled temperature environment. By cooling the coated surface
or the surrounding air, the equipment facilitates the evaporation process,
leading to faster drying or curing times.
Heat Dissipation
- Some coating processes
involve exothermic reactions, where heat is released during curing or chemical
reactions. Process cooling equipment helps to dissipate the excess heat,
preventing overheating and ensuring consistent coating quality. Efficient heat
dissipation prevents issues like blistering, bubbles, or degradation of the
coating due to excessive temperature.
Equipment Cooling
- Process cooling equipment
is also used to cool the equipment or machinery involved in advanced coatings
research and production. Coating equipment, such as spray guns, nozzles, or
rollers, can generate heat during operation. Cooling equipment helps to
maintain the optimal temperature of these components, preventing overheating,
improving their lifespan, and ensuring consistent coating application.
Batch-to-Batch Consistency
- Process cooling equipment
helps to ensure batch-to-batch consistency in advance coatings production. By
maintaining consistent temperature conditions throughout the production
process, the equipment helps to achieve uniform coating properties, colour,
texture, and other performance characteristics. This consistency is crucial for
quality control and meeting specific coating requirements.
Equipment Cleaning
- After coating processes,
equipment and tools used in the production line need to be cleaned to remove
residual coatings or prevent clogging. Process cooling equipment can be used to
provide cooling during the cleaning process. Cooling helps to maintain the
stability and viscosity of cleaning solutions, ensuring effective and efficient
equipment cleaning.
Recirculating Chillers
Recirculating chillers are
widely used in process cooling applications. They are refrigeration systems
that remove heat from a process fluid and maintain a specific temperature
range. Chillers utilise a compressor, condenser, evaporator, and refrigerant to
cool the circulating fluid. Recirculating chillers offer several benefits in
advanced coatings research and production, including:
Precise temperature control:
- Recirculating chillers
provide precise temperature control provide precise temperature control,
allowing researchers and manufacturers to maintain a consistent and accurate
temperature throughout the coating process. This is essential for achieving
desired coating properties, optimising curing or drying conditions, and
ensuring batch-to-batch consistency. The ability to maintain precise temperature
control is particularly important in advanced coatings, where small temperature
variations can significantly impact the final coating quality.
Wide temperature range:
- Recirculating chillers can
cover a wide temperature range. This versatility makes them suitable for
various coating processes that require different temperature conditions.
Whether it’s room temperature coatings, high-temperature curing, or
low-temperature applications, recirculating chillers can be adjusted to meet
the specific temperature requirements of the process.
Efficient heat removal:
- Recirculating chillers
efficiently remove heat generated during the coating process. They circulate a
heat transfer fluid, typically water or specialised fluids, to absorb heat and
maintain the desired temperature. By rapidly and effectively removing excess
heat, recirculating chillers prevent overheating of the coating material or the
production equipment, ensuring consistent coating quality, minimising the risk
of defects, and improving overall process efficiency.
Flexibility:
- Recirculating chillers
offer flexibility to accommodate different research and production scales. They
are available in various sizes and cooling capacities, allowing for easy
adaptation to different coating setups, from laboratory-scale research to
large-scale production facilities. Recirculating chillers can be customised to
meet specific cooling requirements, making them adaptable to diverse coating
processes and equipment.
User-friendly operation:
- Recirculating chillers are
designed for user-friendly operation, making them suitable for both research
and production environments. They often feature intuitive controls, digital
displays, and programmable settings for temperature adjustment and monitoring.
Recirculating chillers are typically self-contained units that are easy to install, require
minimal maintenance, and provide hassle-free operation, allowing researchers
and operators to focus on their coating processes.
Compact and space-saving:
- Recirculating chillers are
compact in size and have a small footprint, making them suitable for
installations where space is limited. They can be placed near to the coating
equipment or integrated into existing setups without occupying excessive space.
The compact design of recirculating chillers ensures efficient use of available
space in research laboratories or production facilities.
Reduced water consumption:
- Recirculating chillers
often incorporate closed-loop systems, which minimise water consumption during
the cooling process. Water is recirculated within the system, reducing the need
for constant water supply and discharge. This water-saving feature is
environmentally friendly and can result in cost savings by minimising water
usage and associated wastewater treatment.
Reliability and safety:
- Recirculating chillers are
designed to provide reliable and safe cooling solutions. They incorporate
features such as automatic temperature control, safety alarms, and system
monitoring to ensure proper functioning and protect against temperature
fluctuations or equipment malfunctions. This reliability and safety contribute
to the overall stability and quality of the coating processes.
Heat Exchangers
Heat exchangers are essential components in advanced coating processes as they facilitate highly efficient heat transfer. They enable the exchange of heat between the heat transfer fluid and process fluid, offering similar advantages to a recirculating chiller. Notably, heat exchangers possess the additional benefits of lower upfront costs and reduced energy consumption. These factors significantly contribute to optimising heat transfer, ensuring precise temperature control, and ultimately elevating the overall quality of advanced coatings. Some of the notable benefits provided by heat exchangers in advanced coatings research and production include:
Efficient heat transfer:
- Heat exchangers facilitate
efficient heat transfer between fluids, allowing for effective cooling or
heating of the coating process. They maximise the exchange of thermal energy,
enabling rapid and controlled temperature changes. Efficient heat transfer
ensures that the coating material experiences the desired temperature
conditions, enhancing the quality and performance of the final coating,
Temperature control and stability:
- Heat
exchangers contribute to temperature control and stability during the coating
process. By regulating the flow of the heat transfer fluid, heat exchangers
help to maintain a consistent temperature within the coating equipment or
system. This temperature stability is critical for achieving uniform coating
properties, controlling the curing or drying process, and ensuring consistent
results from batch to batch.
Flexibility in temperature range:
- Heat exchangers offer
flexibility in temperature range, allowing for both cooling and heating
applications in advanced coatings. They can handle a wide range of
temperatures, from low temperatures for specialised coatings to high
temperatures for curing or drying processes. This flexibility enables
researchers and manufacturers to explore a variety of coating materials and
processes with different temperature requirements.
Customisable configurations:
- Heat exchangers can be
customised to meet specific requirements in advance coatings research and
production. They are available in various configurations which can be tailored
to the specific needs of the coating process. Customisable configurations
ensure compatibility with different coating equipment and enables optimal heat
transfer performance.
Space efficiency:
- Heat exchangers are
designed to be compact and space-efficient, making them suitable for
installations where space is limited. Their compact size allows for easy
integration into existing coating systems or equipment, optimising the use of
available space in research laboratories or production facilities. Heat
exchangers can be installed in confined areas or mounted directly onto coating
equipment, minimising the footprint, and maximising operational efficiency.
Process safety:
- Heat exchangers enhance
process safety in advanced coatings by providing a reliable and controlled
method of heat transfer. They help to prevent overheating of the coating
material, which can lead to quality issues or safety hazards. Heat exchangers
ensure that the coating process remains within the desired temperature range,
minimising the risk of thermal damage, material degradation, or equipment
failures.
Compatibility with various fluids:
- Heat exchangers are
compatible with a wide range of fluids, including water, oils, or specialised
heat transfer fluids. This versatility allows for the selection of the most
suitable heat transfer fluid based on the specific coating requirements. The
compatibility with different fluids ensures that heat exchangers can adapt to
diverse coating processes and materials.
The selection of process cooling
equipment depends on factors such as the required temperature range, cooling
capacity, scalability, space limitations, and specific process requirements.
Different equipment types may be used in combination to provide comprehensive
cooling solutions for advanced coatings research and production.
We are excited to be exhibiting at Advanced Materials 2023. Find us on stand 1418 for a chat about how we can support with your process cooling requirements.
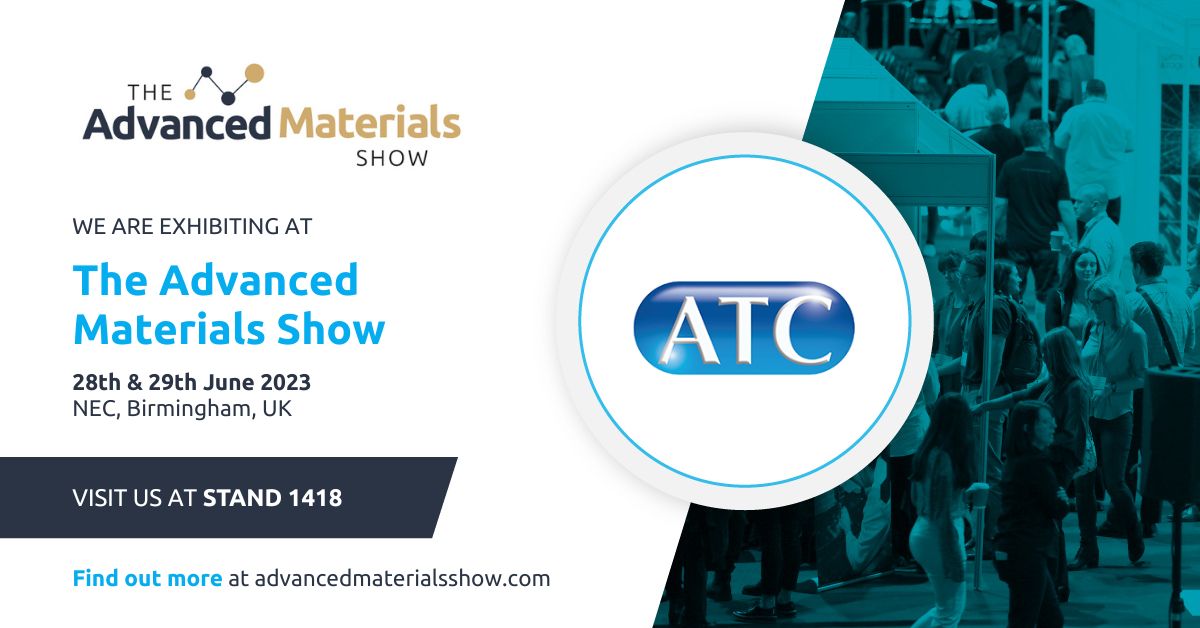